Common mistakes to watch for:
Even a single unit difference in one box disqualifies the entire set from being considered identical. Ensure each box has the exact same items and quantities.
Using features like “Copy Boxes” in InventoryLab can save time, but always double-check that each box truly matches in content and quantity.
Sending only four identical boxes doesn’t meet the requirement. You must have at least five to qualify for the optimized inbound option.
Fix It: How to Meet the 5+ Equal Boxes Rule in InventoryLab
To stay compliant and save time, you can use two key tools in InventoryLab:
If you’re packing mixed SKUs and already created one compliant box, use Copy Box to duplicate it with identical contents. This makes it easier to meet the 5-box minimum without rebuilding from scratch.
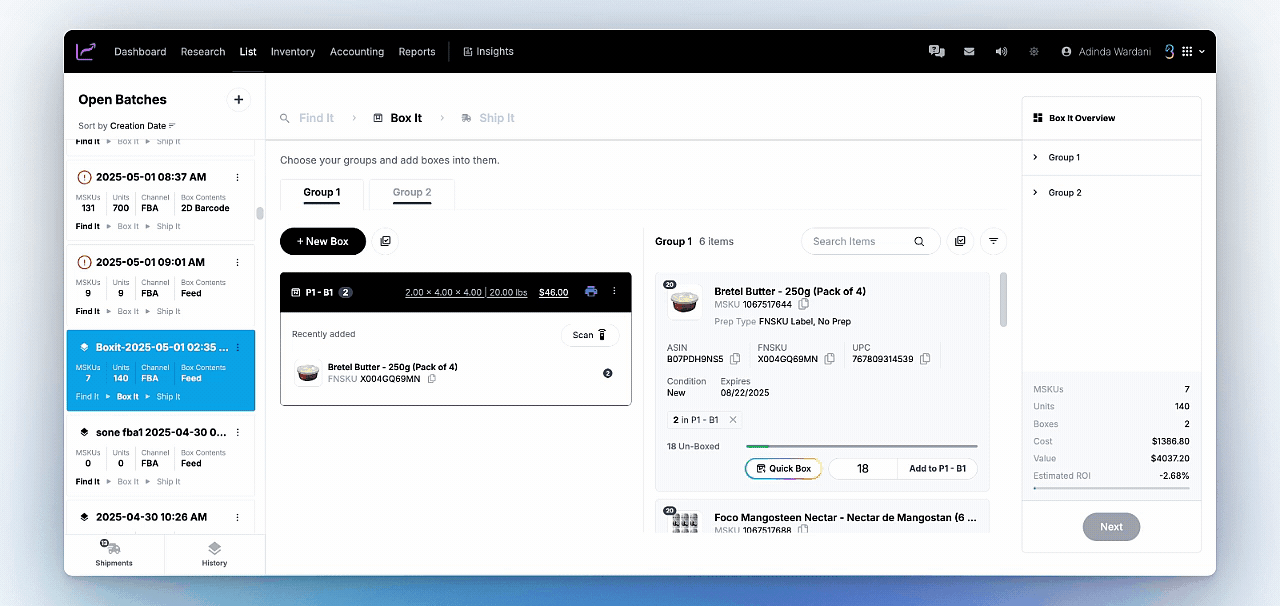
Another alternative feature to use to automatically generate 5 or more identical boxes with the same SKU, quantities, and dimensions. It’s ideal for case-packed shipments or large quantities of a single product.
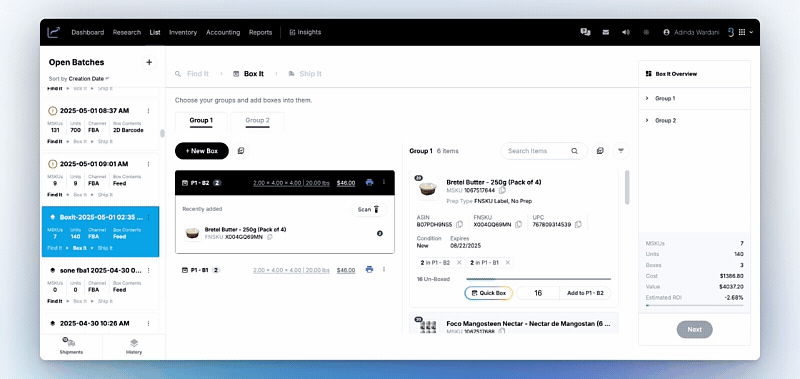
-
Pro Tip:
- Ensure every copied box has exactly the same items, counts, and layout.
- While you can enter box contents manually, Using Quick Box or Copy Box can save time and ensure consistency to avoid any change that breaks the “equal” status.
- If you have fewer than five identical boxes, Amazon won’t apply optimized routing. Use standard packing instead.
Even if the contents are visually the same, Amazon requires exact match in item count, weight, and label sequence. One small change can disqualify the whole shipment.
Sometimes, workflow seems to get stuck in the Box It stage, refusing to move forward even when everything looks correct.
Here’s what might be causing it:
- Not all SKUs are assigned to a box
Even one missing SKU can block the workflow. If a product isn’t fully assigned, the system won’t let you proceed.
If you’ve created boxes that don’t contain any SKUs, or forgot to delete unused boxes, that can trigger errors.
- Glitches or browser freezes
Occasionally, the session can freeze or hang mid-process, especially if you’re switching tabs or using auto-fill extensions (e.g., ad blockers, autofill tools) that sometimes interfering with session saving.
- Reopening a saved batch too soon
If the workflow was closed or submitted too quickly, reopening it might not refresh everything properly, causing a stuck state.
Quick Fix
If the workflow gets stuck, close the batch first, then head to List → History and use the Restore Workflow option to pick up where you left off.
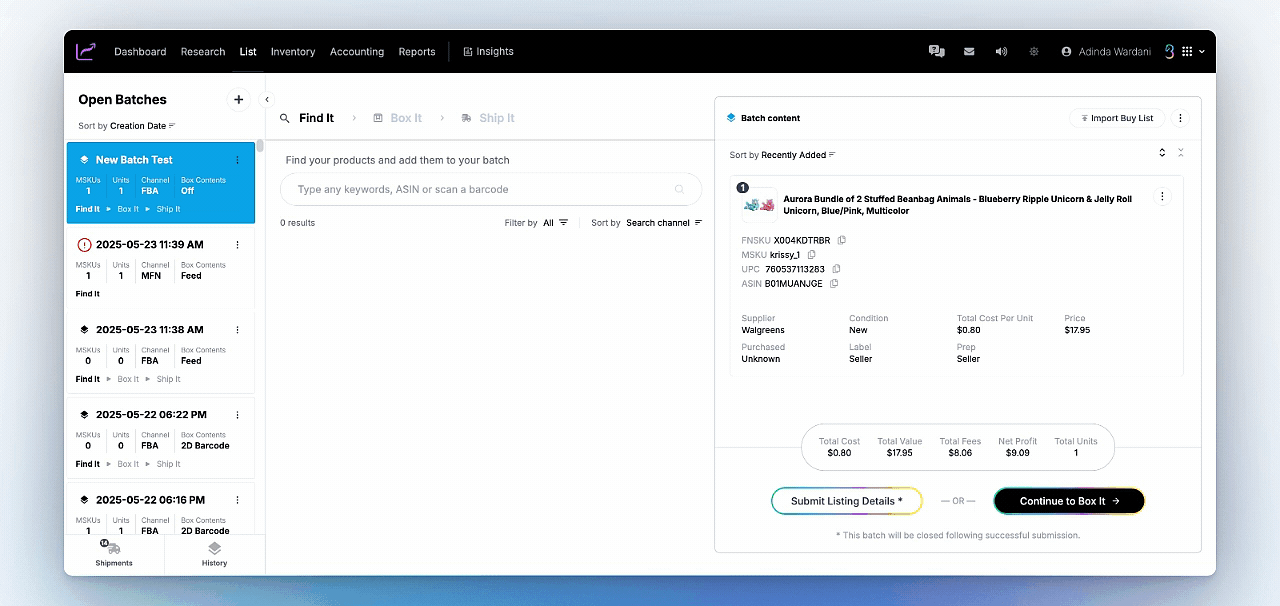
If it’s still stuck or unresponsive, don’t be afraid to back out and re-create the workflow. Your product data is often still saved.
This is one of the most common (and confusing) moments during the shipping process.
You finish packing your boxes and assign SKUs in InventoryLab. You see Box 1, Box 2, Box 3 clearly in your Box Content section.
Then you print your shipping labels… and instead of “Box 1,” your labels say P1, P2, P3.
You’re left wondering:
Does Box 1 = P1? Or did something get mixed up?
Here’s a side-by-side comparison of what you’ll see in InventoryLab vs what you’ll get from Amazon:
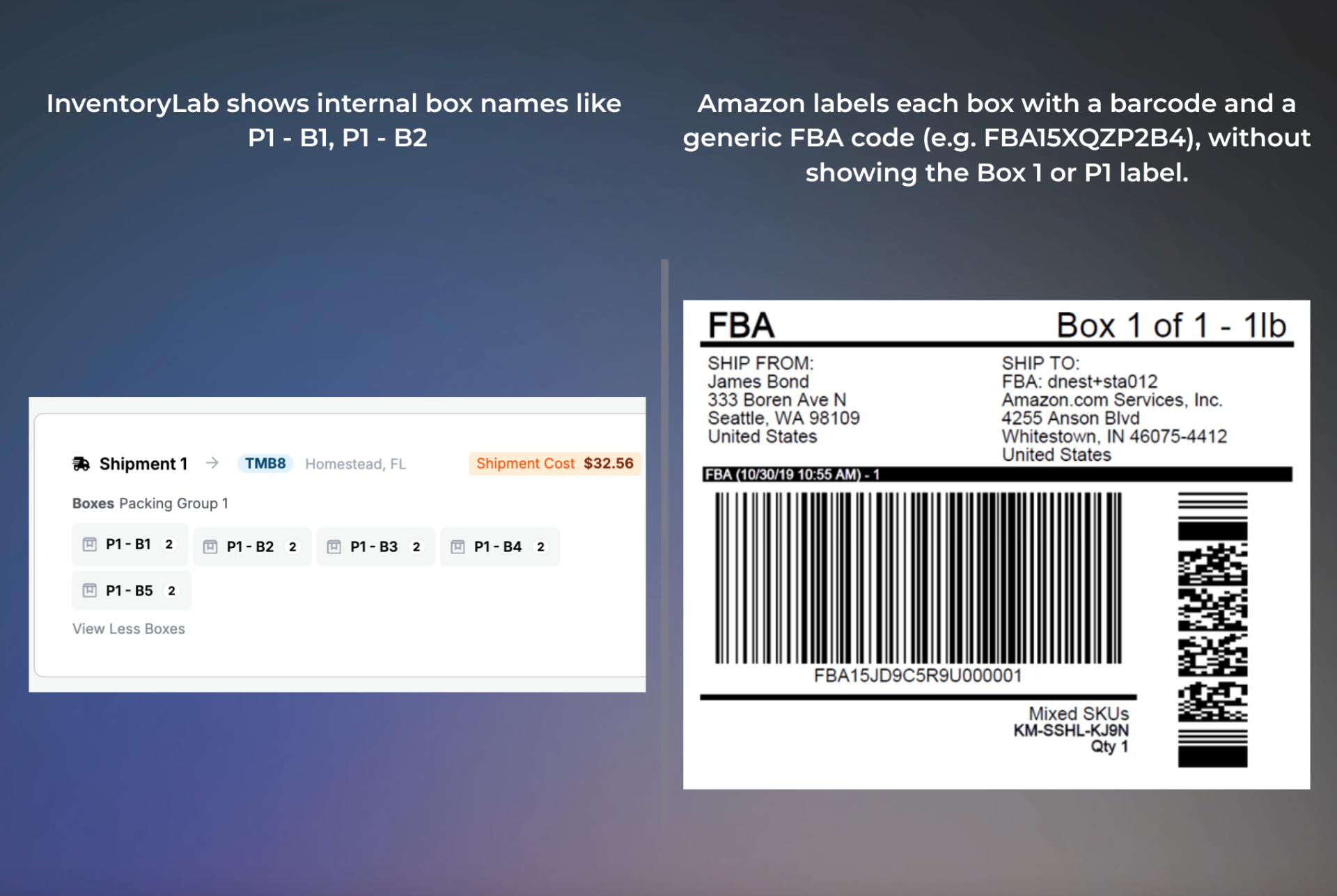
Why It Happens
-
Box numbers in InventoryLab (Box 1, Box 2, etc.) are internal references to help you track which SKUs went into which box.
-
P1, P2, P3 are Pack Group identifiers. These labels correspond to the Pack Groups you created in InventoryLab. Once box contents are submitted to Amazon, each group is matched to a specific box for labeling.
-
If the box content isn’t submitted correctly, or if you made changes after submitting, these numbers can get out of sync.
What This Confusion Can Lead To
-
Mislabeled boxes (Box 2 accidentally gets P3 label)
-
Amazon thinking the box contents don’t match what was submitted
-
Receiving delays or stranded inventory
-
Wasted time repacking or reprinting labels
How to Fix and Avoid the Mix-up
To avoid issues, complete the entire Box It and Ship It process within InventoryLab; don’t switch back and forth with Seller Central unless absolutely necessary. When you’re ready, purchase your shipping labels directly from InventoryLab to automatically send the box content details to Amazon.
After printing, double-check that the contents of each box match the label. Box 1 should align with P1, Box 2 with P2, and so on. Don’t reorder or rename boxes after transmitting the information, as this can cause mismatches between your boxes and Amazon’s records.
If you’re ever unsure, try to print the label beforehand during the Box It stage. This will minimize confusion before moving to the next stage.
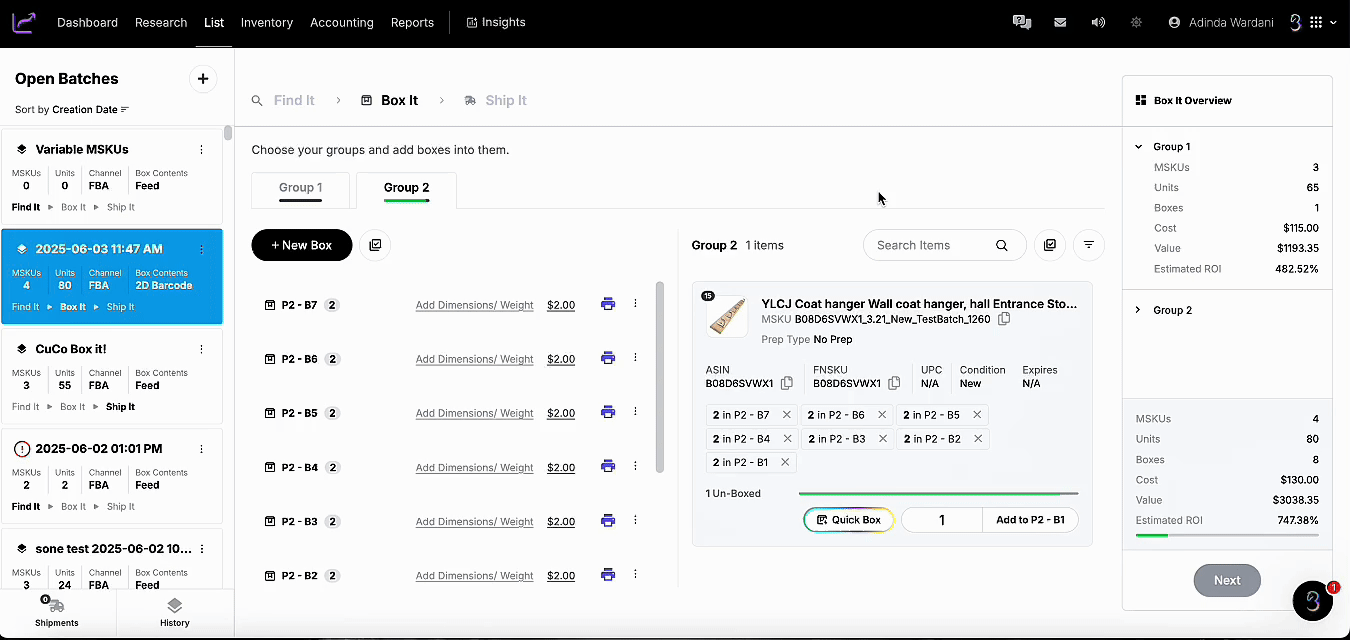
The Box It stage can be tricky at first, but most issues boil down to a few core causes:
-
Not understanding Amazon’s 5+ equal box requirement
-
Skipping the logic behind auto-assigned Pack Groups
-
Editing boxes too late or across different systems
To avoid common issues, make sure you:
-
Batch similar SKUs together
-
Use Quick Box and Copy Box to maintain consistent packing
-
Complete the process inside InventoryLab without switching to Seller Central
You’ll avoid the vast majority of shipment issues and save yourself serious time and frustration.
Box It doesn’t have to be a bottleneck. With the right steps and the right tools you’ve got this!
If you still need help, reach out to InventoryLab Support at support@inventorylab.com and we’re happy to walk you through your workflow or help troubleshoot any stuck shipment.
You’re not the only one who’s ever been stuck at Box It and you don’t have to figure it out alone!